湛江爱步精益咨询精益生产人才绩效管理
整顿是在整理的基础上,对现场物品进行科学合理的布置和标识。通过整顿,企业可以确保员工能够快速准确地找到所需的物品,减少了寻找时间和精力的浪费。同时,整顿还有助于建立良好的工作秩序和作业习惯,使员工能够按照既定的流程和规范进行操作,提高了工作效率和质量。清扫是保持工作环境清洁的重要手段。在6S管理中,清扫不仅*是简单的打扫卫生,更是对设备、工具和工作场所进行深度清洁和保养的过程。通过定期清扫,企业可以消除污垢、灰尘和油渍等污染源,保持设备的正常运转和延长使用寿命。同时,清扫还能提升员工的工作积极性和责任感,使他们更加珍视和爱护自己的工作环境。减少浪费:精益生产管理通过避免过度加工,能够有效提高生产效率和产量,减少整个生产过程中的废物量。湛江爱步精益咨询精益生产人才绩效管理
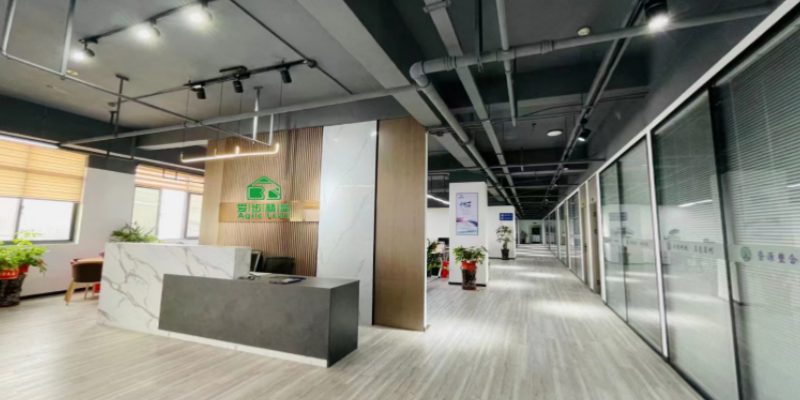
看板管理是一种以看板为主要工具,实现生产过程中信息传递和控制的管理方法。看板通常是一种卡片、标识牌或电子显示屏等,上面记录着生产指令、物料需求、生产进度等信息。作用信息传递:看板作为信息载体,将生产指令、物料需求等信息从一个环节传递到另一个环节,确保生产过程的顺畅进行。生产控制:通过看板的数量和流动,可以控制生产的节奏和进度,避免过度生产或生产不足。减少浪费:看板管理有助于实现准时化生产,减少库存、等待时间和搬运等浪费。提高透明度:使生产过程中的信息更加透明,便于管理人员和员工了解生产情况,及时发现问题并采取措施。宁波爱步精益生产提质增效推行精益的5个步骤,第5个步骤的基础,是保障全员积极参与改善。
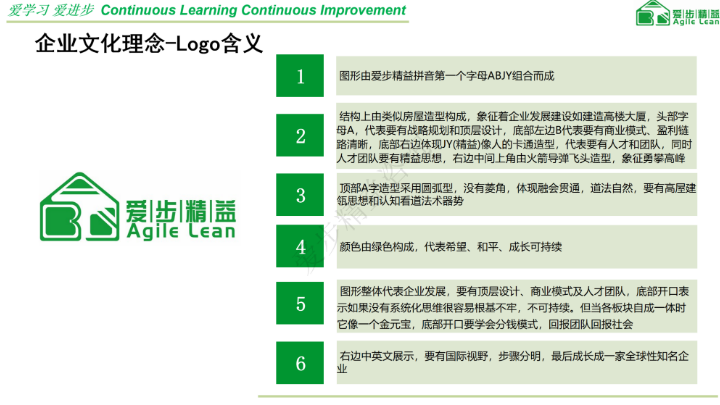
可视化管理是精益生产中的一种重要管理手段。通过将生产现场的信息实时、直观地呈现给管理者和员工,有助于他们迅速掌握生产状况,及时发现问题并采取有效措施。在精益生产中,可以运用看板、图表等可视化工具对生产进度、质量状况、设备状态等信息进行实时更新和展示。同时,建立信息共享平台,实现各部门之间的数据共享和协同工作,可以进一步提高管理效率和决策水平。通过可视化管理,企业能够及时发现和解决生产过程中的问题,避免生产延误和质量损失。同时,员工也能够更加清晰地了解自己的工作目标和任务,提高工作效率和责任心。
提高生产效率通过消除浪费、优化生产流程、提高设备利用率等方式,可以显著提高生产效率,降低生产成本。提高产品质量精益生产强调质量是生产出来的,而不是检验出来的。通过实施自动化、建立质量控制体系等方式,可以提高产品质量,减少不良品的产生。降低库存准时化生产和拉动式生产方式可以减少库存,降低库存成本,提高资金周转率。增强企业竞争力精益生产可以提高企业的生产效率、产品质量和降低成本,增强企业的竞争力,使企业在市场竞争中处于有利地位。精益生产是一种先进的生产方式,它可以帮助企业提高生产效率、产品质量和降低成本,增强企业的竞争力。在实施精益生产的过程中,企业应该根据自身的实际情况,选择合适的方法和工具,制定切实可行的改进计划,并持续不断地进行改进和完善。企业应当注重员工的技能培养,提高员工的专业技能和素质水平。
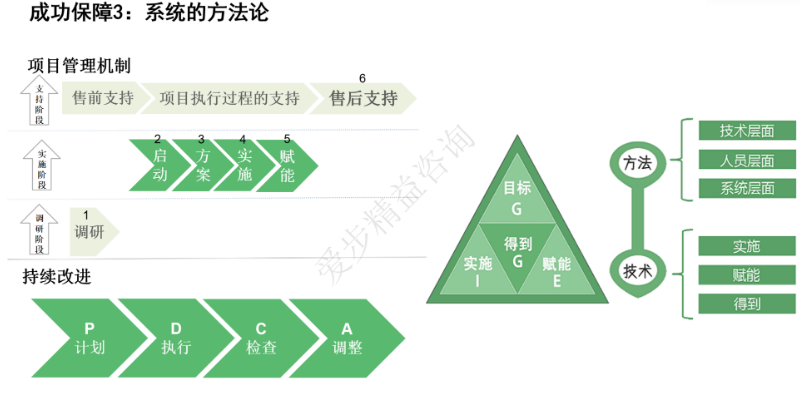
精益生产指特别的生产组织、管理方式 [1-3]精益生产有两大特征;准时生产、全员积极参与改善 [2-6]正是因为两大特征,才能“以越来越少的投入获取越来越多的产出 [2]”
精益生产有两大特征;准时生产、全员积极参与改善准时生产1、准时制是由大野耐一领导、首先由丰田公司发展出来的。准时制的目的是要消除各种没有附加价值的动作,同时达成一个去芜存菁的生产体系,以便更具弹性地去适应顾客订单的需求变化。 [5]2、推行精益主要改善活动之一,是准时制。 [5]3、精益生产又称准时生产、准时制、JIT [5]4、杰弗瑞·莱克在他所著的《丰田模式》中论到丰田模式的14项原则 [3]第二项;建立连续的作业流程第三项;使用拉动式生产方式这两项都是“准时生产”5、詹姆斯P.沃麦克、丹尼尔T.琼斯在他们合著的《精益思想》中,把推行精益生产定义为5个步骤; [2]第三(建立连续的作业流程)、第四(拉动),都指准时制全员积极参与改善1、推行精益主要改善活动之一,是提案建议制度,保障全员积极参与改善 [5]2、帮助人们积极参与改善,是推行精益的根本 [4]3、推行精益的关键,是建立一套系统,保障全员积极参与改善 [6]4、推行精益的5个步骤,第5个步骤的基础,是保障全员积极参与改善 [2] 制定有效的沟通策略:生产管理包括评估员工的绩效、调整流程和程序以提高效率、为团队设定目标等。韶关精益生产人才绩效管理
要有大量多能工,就要有快速培养大量多能工的工具;湛江爱步精益咨询精益生产人才绩效管理
在实施七大浪费管理的过程中,企业需要建立一套完善的管理制度和监督机制。这包括制定明确的浪费识别标准、建立持续改进的文化氛围、开展定期的浪费检查和评估等。通过这些措施,企业可以及时发现和消除浪费现象,确保生产过程的效率和效益。七大浪费管理是企业实现精益生产的重要一环。通过识别并消除这些浪费,企业不仅可以降低成本、提高效率,还可以提升产品质量和客户满意度。然而,浪费管理并非一蹴而就的过程,需要企业长期坚持并不断改进。因此,企业应将七大浪费管理纳入日常管理中,使其成为企业文化的一部分,从而推动企业持续、稳健的发展。湛江爱步精益咨询精益生产人才绩效管理
上一篇: 丽水厦门爱步精益咨询精益生产流程标准化
下一篇: 衢州如何培训6s包括哪六个方面